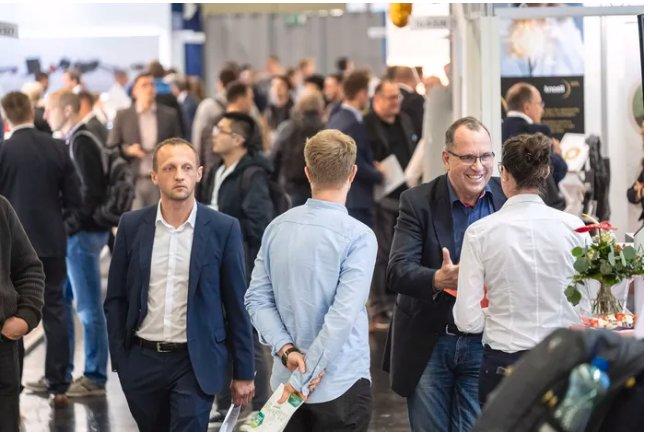
Produktionsschritt 1: Das Material
Steht die Konzeption und Planung eines Endproduktes für die Medizintechnik, ist die Ausgangsbasis das Rohmaterial. Den Anfang macht Forécreu, ein weltweit führender Hersteller von kanülierten Rundstangen aus Edelstahl, Spezialstahl und Titan, die zum Beispiel für die Fertigung von Schrauben, Nägeln, Bohrern oder chirurgischen Fräsern verwendet werden. Die Produktionsstraße zeigt, wie das Rohmaterial mit bereits bestehender Kanülierung be- und weiterverarbeitet wird. „Die Kanülierung ist ein sehr komplexer Prozess, aber essentiell, um die Werkzeuge so einsetzen zu können, dass man sie über die Führungs-Drähte in die exakte Position und Anwendung bringen kann“, erklärt Markus Naumann, Area Sales Manager von Forécreu.
Produktionsschritt 2: Das Bauteil
Die Arbeitsschritte sind bei der Entstehung wie bei jedem anderen Drehteil aufeinander abgestimmt und verlaufen gleich: „Das vorbereitete Material kommt bei uns an. Anhand einer Zeichnung des gewünschten Bauteils wird die Stückzeit im Vorfeld berechnet und anschließend das Drehteil an der CNC-Maschine programmiert. Über komplexe Einzelschritte kommt am Ende das zu 100 Prozent fertige Bauteil heraus“, fasst Sascha Gersmann, Marketingleiter bei der Citizen Machinery Europe GmbH zusammen. Die Herstellung eines Drehteils durch hochmoderne Citizen Maschinen, erfolgt effizient und schnell. Die eigens von Citizen entwickelte LFV-Technologie (Low Frequency Vibration Cutting) optimiert durch definierten Spanbruch die Drehbearbeitung des Bauteils, vermeidet Aufbauschneiden, schont das Werkzeug und ist bei nahezu allen Metallen sowie bei Kunststoffen anwendbar.
Produktionsschritt 3: Applikation von Kunststoffen
Ist das Metallteil gefertigt, ist der nächste Schritt der Einsatz von Kunststoffen, um das Teil beispielsweise mit einem Griff zu versehen. Das Unternehmen Gindele GmbH, Spezialist für Formenbau und Kunststoffspitzguss, zeigt diesen Herstellungsschritt in der Produktionsstraße der MedtecLIVE with T4M und verwendet dafür die Spritzgusstechnik: „Wir umspritzen das Bauteil. Dafür wird der Einleger in diesem Fall händisch in eine Negativform eingelegt, die dann mit Kunststoff aufgefüllt wird“, erklärt Matthias Gindele, Geschäftsführer von Gindele GmbH. Der Standardprozess gehört zu einem Großteil der Produktionsstraßen in der Medizintechnik und ist daher ein essenzieller Bestandteil der Darstellung.
Produktionsschritt 4: Die Reinigung
Um Verunreinigungen aus Produktionsprozessen zu entfernen, aber auch die weiterführende Bearbeitung zu ermöglichen, ist es wichtig, dass das entstehende Produkt immer wieder gereinigt wird. Mehrere Reinigungsschritte wie Entfettung, Vorreinigung und Zwischen- und Endreinigung können dabei angewendet werden. Dafür wird von der KKS Ultraschall AG, das einzige Unternehmen mit Expertise im Outsourcing und Anlagenbau zur ultraschallgestützten Reinigung sowie zur Veredelung von Oberflächen, eine ultraschallgestützte Verfahrenstechnik eingesetzt. Durch den Einsatz von Ultraschall in Kombination mit wässrigen Medien werden höchste Reinheitsgrade bei relativ kurzen Reinigungszeiten erreicht. Auch bei kompliziert geformten und filigranen Bauteilen mit strukturierten, porösen Oberflächen sowie kleinsten Nuten und Bohrungen wird ein hoher Reinheitsgrad erreicht. Durch die Automatisierbarkeit und eine erhöhte Produktivität kann die Reinigung zu einem hohen Grad optimiert werden und das Produkt ist bereit für den nächsten Fertigungsschritt.
Produktionsschritt 5: Das Markieren durch den Laser
Nach der Reinigung folgt der nächste Fertigungsschritt: die Lasermarkierung. Warum das wichtig ist? Es schützt das Produkt, den Anwendenden und die Patientinnen und Patienten. Denn das Produkt muss eindeutig gekennzeichnet sein, zum Beispiel mit einem UDI-Code (Unique Device Identification) oder einem Haltbarkeitsdatum. „Ein Vorteil der Markierung mit FOBA ist die Markierung ohne kostspielige Aufnahmen. Unsere automatisierte Markierfunktion MOSAIC erkennt die Lage des Artikels und richtet die Markierung entsprechend aus “, erklärt Christian Söhner, Global Vertical Manager Medical bei FOBA Laser Marking + Engraving. Für FOBA, international führenden Hersteller und Anbieter von innovativen Präzisionssystemen zum Markieren und Gravieren mit Laser, ist Söhner langjähriges Mitglied im Messebeirat und war maßgeblich an der Idee und der Umsetzung der Produktionsstraße beteiligt. „Da die Markierung am Ende des Prozesses stattfindet, sind Fehlerfreiheit und Zeichenqualität enorm wichtig zur Vermeidung von Ausschuss. Dabei hilft die im Markierkopf integrierte Kamera“, ergänzt Söhner. Diese Entwicklung verkürzt den gesamten Produktionsschritt außerdem und sorgt für mehr Flexibilität. Der Laser-Vorgang dauert gerade einmal zwei bis vier Sekunden, je nach Anwendung.
Produktionsschritt 6: Die Passivierung und Endreinigung
Bevor das gefertigte Produkt nun verpackt werden kann, muss die zuvor lasermarkierte Oberfläche passiviert und endgereinigt werden. Die Passivierung schützt das Grundmaterial vor korrosiver Zerstörung (Passivschicht). Nach dem Passivieren werden die Teile intensiv mit Wasser hoher Qualität (Osmose-Wasser, VE-Wasser) gespült und sofort getrocknet. Im Regelfall orientieren sich die angewandten Oberflächenbehandlungs-Verfahren, inklusive der Vor- und Nachbehandlung beim Passivieren von Bauteilen, den Empfehlungen der Normen ASTM A380 und ASTM F86. Die Sicherheit der Patient*innen und Produktanwender steht an oberster Stelle, weshalb es notwendig ist, dass das Produkt entsprechend hohe Reinheitsanforderungen erfüllt. Die Passivierung respektive Endreinigung ist somit essenziell für jede Produktionsstraße.
Produktionsschritt 7: Die Verpackung
Ist das Endprodukt gereinigt, kann es fachgerecht verpackt werden. „Für die Verpackung können wir von der Folie bis zum fertig verpackten Produkt alles liefern. Dafür haben wir das Rohmaterial, Blister, Deckel, Beutel und eine Siegelmaschine“, erklärt Felix Neidhart, Leiter des Vertriebs bei der Medipack AG, einem Schweizer Systemlieferant für Medizinalverpackungen. Für die Verpackung wird die Ware in einen Blister gelegt und mit einem Siegeldeckel verschweißt. Wichtige Kriterien sind dabei, dass die Verpackung leicht zu öffnen ist, das Produkt schützt und steril hält. Sowohl die Siegelmaschine als auch den Verpackungsvorgang sind Besonderheiten, die in der Produktionsstraße sichtbar und anschaulich gemacht werden.
Mehrwert für die Besucher
Die Produktionsstraße auf der MedtecLIVE with T4M zeigt, was Zusammenarbeit möglich macht und welche Fertigungsschritte zu einem medizinischen Endprodukt gehören. „Ziel ist es, dass die Besucher Neues lernen und wir ihre konkreten Fragen beantworten, vielleicht sogar Knoten lösen können“, wünscht sich Söhner. Denn was heutzutage möglich ist, kann die Produktionsdauer anderer Hersteller verkürzen oder anderweitig effizienter gestalten. „Schön wäre es, wenn die Besucher das Zusammenspiel der Hersteller mitnehmen, sich Impulse holen und so auch ihre eigene Produktion verbessern können“, fasst Niklas Kuczaty, Geschäftsführer der VDMA Arbeitsgemeinschaft Medizintechnik, zusammen. Durch das hautnahe Erleben der Prozesskette, die für eine Produktion benötigt wird, können die Besonderheiten der Medizintechnik mit allen Sinnen wahrgenommen werden. Auch Gindele sieht darin ein Vorteil: „Wir können mit der Produktionsstraße alle Besucher mitnehmen und jeder kann sich einbringen. Das ist ein Treffpunkt mit Mehrwert und Erlebnisfaktor.“
Das Projekt Produktionsstraße bei der MedtecLIVE with T4M macht Medizintechnik greifbar und verständlich. „Das ist wichtig, denn nur, wenn man einen Prozess in der Ganzheit versteht, kann man ihn optimieren. Deswegen war es uns so wichtig, den Besuchern die persönliche Vernetzung vor Ort mit den verschiedenen Herstellern zu ermöglichen und Lösungen erlebbar zu machen. Das ist auch das, was Messen ausmacht – Technik zum Anfassen. Dafür bildet die Veranstaltung eine Plattform und den Rahmen für die Entwicklung und Umsetzung neuer Ideen, die die Branche weiterbringen“, so Christopher Boss.
Über MedtecLIVE with T4M
Die Messe MedtecLIVE with T4M ist das führende europäische Frühjahrs-Event der Medizintechnik und findet jährlich abwechselnd in Stuttgart und Nürnberg statt. Die Veranstaltung deckt die gesamte Wertschöpfungskette ab und verbindet dabei die wichtigsten Medizintechnikregionen in Deutschland. Hier treffen Entscheider der Inverkehrbringer und OEMs auf die wichtigsten Zulieferer der Medizintechnik.
NürnbergMesse GmbH
Messezentrum
90471 Nürnberg
Telefon: +49 (911) 8606-0
Telefax: +49 (911) 8606-8228
http://www.nuernbergmesse.de
Telefon: +49 (911) 977916-16
Fax: +49 (911) 977916-19
E-Mail: press_medteclive@nuernbergmesse.de